Porosity in Welding: Identifying Common Issues and Implementing Finest Practices for Avoidance
Porosity in welding is a prevalent issue that usually goes unnoticed till it causes substantial problems with the integrity of welds. In this discussion, we will certainly explore the key aspects contributing to porosity formation, examine its destructive results on weld efficiency, and go over the best techniques that can be embraced to decrease porosity occurrence in welding procedures.
Typical Root Causes Of Porosity
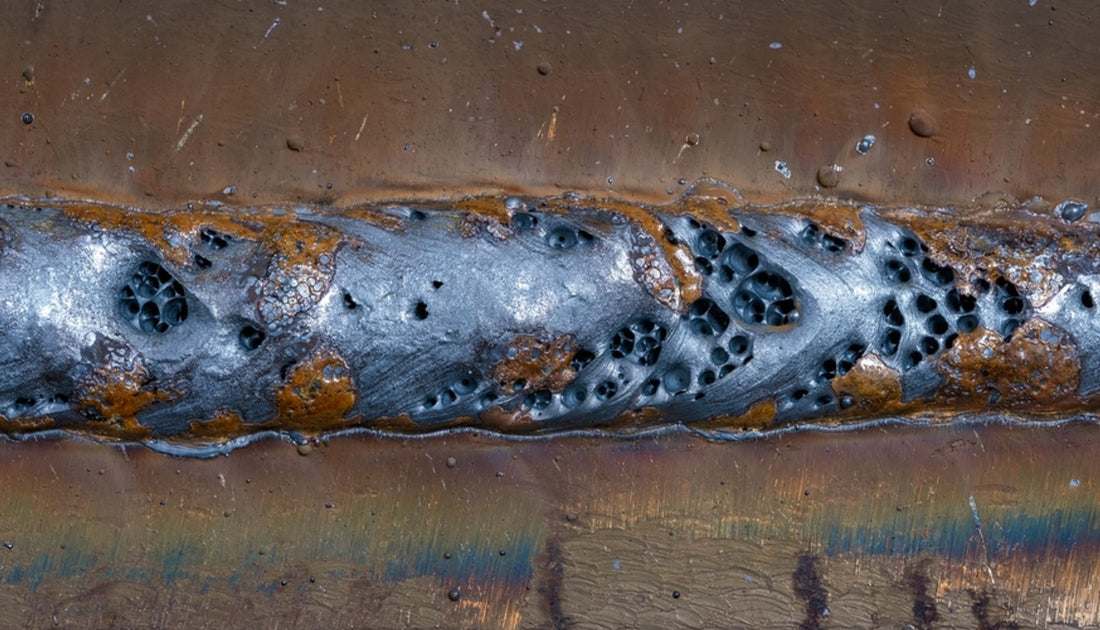
Using filthy or wet filler products can introduce contaminations right into the weld, contributing to porosity issues. To alleviate these typical reasons of porosity, complete cleaning of base metals, correct securing gas option, and adherence to ideal welding specifications are essential methods in accomplishing high-quality, porosity-free welds.
Influence of Porosity on Weld Top Quality

The presence of porosity in welding can significantly jeopardize the structural stability and mechanical homes of bonded joints. Porosity produces gaps within the weld metal, damaging its general strength and load-bearing ability.
Welds with high porosity levels tend to show lower impact stamina and lowered capacity to deform plastically prior to fracturing. Porosity can hinder the weld's ability to efficiently transmit forces, leading to premature weld failing and possible security hazards in important frameworks.
Ideal Practices for Porosity Prevention
To improve the architectural stability and high quality of welded joints, what specific steps can be carried out to minimize the occurrence of porosity during the welding process? Utilizing the right welding method for the details material being welded, such as changing the welding angle and gun position, can further avoid porosity. Regular assessment of welds and instant removal of any type of issues recognized during the welding procedure are necessary methods to protect against porosity and create high-grade welds.
Importance of Correct Welding Techniques
Applying proper welding techniques is vital in guaranteeing the architectural stability and quality of welded joints, building upon the foundation of reliable porosity prevention procedures. Excessive heat can lead to enhanced porosity due to the entrapment of gases in the weld swimming pool. Furthermore, using the ideal welding specifications, such as voltage, present, and travel speed, is important for attaining audio welds with minimal porosity.
Additionally, read this article the option of welding procedure, whether it be MIG, TIG, or stick right here welding, should straighten with the details demands of the project to ensure optimal results. Correct cleaning and prep work of the base metal, as well as selecting the ideal filler material, are additionally crucial elements of competent welding techniques. By sticking to these finest methods, welders can reduce the danger of porosity development and produce premium, structurally audio welds.

Evaluating and Quality Control Procedures
Quality control steps play an essential role in validating the integrity and reliability of bonded joints. Evaluating treatments are vital to spot and protect against porosity in welding, making sure the toughness and longevity of the final item. Non-destructive screening approaches such as ultrasonic screening, radiographic screening, and visual evaluation are frequently employed to recognize prospective flaws like porosity. These techniques permit the analysis of weld high quality without compromising the integrity of the joint. What is Porosity.
Post-weld inspections, on the other hand, analyze the final weld for any kind of flaws, including porosity, and verify that it meets defined standards. Implementing a thorough high quality control strategy that consists of extensive testing procedures and evaluations is paramount to reducing porosity problems and making certain the overall top quality of bonded joints.
Final Thought
To conclude, porosity in welding can be a common issue that impacts the quality of welds. By identifying the typical root causes of porosity and applying finest practices for avoidance, such as correct welding methods and testing measures, welders can make sure excellent quality and dependable welds. It is important to focus on avoidance approaches get redirected here to decrease the event of porosity and keep the honesty of bonded structures.